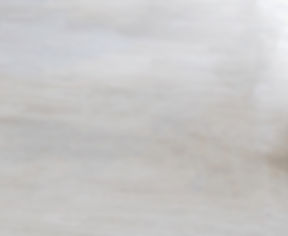



TRAINING
SERVICES

On site and On-line Trainings to improve your Company Performance
Our team of experts will be gladly to assist you on any question regarding training of the following topics:





EXPERIENCE OUR ROLTO QS ON- LINE PLATFORM
ON LINE..?


Quality Management Systems
ISO 9001 Fundamentals
The aim of this course is to provide students who have an existing, basic knowledge of, or experience in, quality management with an understanding of the management systems approach and the requirements of ISO 9001, and to provide a basis for students who wish to become internal auditor.
Internal Auditor training
The aim of this course is to provide students with the knowledge and skills required to perform an internal audit of part of a quality management system based on ISO 9001 (or equivalent), and report on the effective implementation and maintenance of the management system in accordance with ISO.



SIX SIGMA Training
Six Sigma Yellow Belt Training
A Six Sigma Yellow Belt is a individual who is versed in the basics of the Lean Six Sigma Methodology who supports improvement projects as a part of a team or conducts small projects on a part time basis. A Six Sigma Yellow Belt possesses an understanding of the aspects within the phases of DMAIC..
Six Sigma Green Belt Training
A Six Sigma Green Belt is a professional who is well versed in the Six Sigma Methodology who both leads or supports improvement projects, typically as a part-time role. A Six Sigma Green Belt possesses a thorough understanding of all aspects within the phases of D-M-A-I-C. They understand how to perform and interpret Six Sigma tools..
SPC (Statistical Process Control)
Provides sound information upon which to make decisions. It allows process performance tracking on a real-time basis, allowing for corrective actions to be taken before failure occurs



Problem Solving Techniques
8 D (Eight Disciplines) Training
8D Training covers the eight disciplines (8D) model used in advanced problem solving. 8D training covers the approach typically employed by quality engineers to identify, correct, and eliminate recurring problems as part of product and process improvement.
RCA (Root Cause Analysis)
RCA is applied to methodically identify and correct the root causes of events, rather than to simply address the symptomatic result. Focusing correction on root causes has the goal of entirely preventing problem recurrence
FMEA Training
Failure Modes and Effects Analysis (FMEA) is a valuable tool for preventing failure in both product and process design. FMEA is not a form to be completed alone by the responsible engineer after the design has been completed. FMEA should be planned to coincide with product development when risks can be mitigated to an acceptable level in advance of product or process release..

